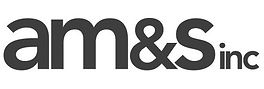
CNC Machine Shop & Assembly House
AS9100D Quality Management System
email: controller@ams-mfg.com 408.396.3027
foreign object debris (fod) prevention @ AM&S
Foreign Object Debris is a major concern in the aviation, space, and defense industry and, thus, a major concern at AM&S. Maintaining a clean production facility has several benefits including reduction of production delays and final product quality. As a result, AM&S' FOD preventative program strives for a debris-free environment for its employees and customers.
​
​
What Qualifies as a FOD Threat?
In a precision machining facility, almost everything and anything found on the production floor, inspection room and offices can be considered a FOD theat. Example of such items are:
​
1. Everyday items: pens, pencils, paperclips, staples, tape, scraps of paper...
2. Industrial waste: metal/plastic chips, rags, grease, cleaning solvent, lubricants...
​
These items can fall into machinery or parts creating a safety hazard and potential product failure for our customers.
Striving for a FOD Free Environment
1/ CLEAN AS YOU GO ; This applies to all surfaces and every space near the product we are making during all phases of manufacturing, testing, transportation and storage. It includes prompt removal of debris, clutter and dirt to minimize the threat. Every member of our team is trained to clean as they work.
​
2/ TOOL ACCOUNTABILITY ; Any tool, regardless of size or weight, can present a threat. Tools are organized in kits for each project and reviewed when they go in and out of the production floor. Each machine has a specified worktable where tools are kept while the jobs are set up and run. The list of tools for a project includes the measurement gages needed to verify the part dimensions, such as micrometers, calipers, and pin gages. Every member of the production team is trained to be accountable for the tools they are using on a project so they don’t end up where they shouldn’t be.
​
3/ HARDWARE ACCOUNTABILITY ; Like tools, small parts and loose hardware can pose a significant FOD risk in manufacturing environments. In a machine shop, this includes items like set screws and fasteners used in setting up the machine. These items can also be kitted so that team members have the amount of hardware necessary for any given task.
​
4/ REPORT MISSING, LOST, AND FOUND ITEMS ; Every team member knows they are responsible for reporting lost or missing hardware, tools, or even personal belongings. Our focus is on proactively preventing damage and improving safety, not on punishing mistakes. The sooner the issue is reported, the less likely damage or injury can occur.
​
5/ MANAGEMENT AUDITS AND REVIEWS ; Our management team is trained to do spot inspections and regular reviews. These checks on our process provide additional insight into problem areas and reinforce the importance of an ongoing effort to maintain the best environment for production areas that reduce injuries and produce exceptional quality.
​
Striving for a FOD Free Environment
Area Designations
1/ FOD AWARENESS - BLUE (LOWEST LEVEL)
​
The principle awareness area is manufacturing. Employees must minimize FOD exposure and follow guidelines.
-
Practice Clean-As-You-Go
-
Practice good housekeeping standards
-
Standard tool accountability recommended
-
Secure Jewelry and Badges
-
Use Protective Dunnage for Parts (cover if possible)
​
2/ FOD AWARENESS - YELLOW (MEDIUM LEVEL)
​
These areas are at medium risk level for FOD incidents. The principle areas include: tumbling, spinner tumbling, washing, in-process inspection, final Inspection, and packaging. In FOD – Controlled areas, there is a medium potential for entrapment or migration of FOD into hardware. Exposure to FOD can degrade form fit or function of components, systems or assemblies. Expectations are that employees follow these guidelines.
-
Operation shall inspect 100% of part for FOD
-
Use Protective Dunnage for Parts (cover if possible)
​
3/ FOD AWARENESS - RED (HIGHEST LEVEL)
​
In critical areas, there is a high-risk level for FOD Incidents. Principle process areas include: assembly manufacturing, traveler/control plan, final inspection, in-process inspection, and shipping. Work in an FOD Critical Area must comply with requirements.
-
Special designated area
-
Operation shall inspect 100% of parts or assembly for FOD
-
Practice Clean-As-You–Go
-
Practice superior housekeeping standards
-
Strict tool accountability enforced
-
No food or beverages allowed